Toz boya üretiminde, ürün kalitesinin devamlılığının yanı sıra karlılık oranında da artışın sağlanabilmesi için vibrasyonlu ( titreşimli ) elek ekipmanlarına yönelik isteklerde önemli artışlar oldu.
Toz Boya Endüstrisi
Son yıllarda toz boya endüstrisi Amerika ve Avrupa’da önemli bir ölçüde büyüdü. Lastik ve süspansiyon sistemleri gibi otomotiv parçalarından, petrol ve gaz borularına, çamaşır makineleri ve mikrodalga fırınları gibi beyaz eşyaya kadar birçok yeni pazarlar, yüksek performanslı boya kaplamadan fayda sağlayabilmek adına piyasada yerlerini aldı.
Üstün dayanıklılığı, çatlamaya ve çizilmeye olan direnci, spreyleme sistemlerindeki basit yöntem sayesinde geri dönüşümü ile toz boya, geleneksel sıvı boya yönteminden çok daha üstün özelliklere sahip olduğunu kanıtlamıştır.
Fakat son bir kaç yılda, durgunlaşan pazar ve yükselen hammadde maliyetleri nedeni ile büyümenin devamlılığını sağlayabilmek ve sağlıklı bir karlılık elde edebilmek için imalatçılar artık faaliyetlerini her açıdan daha detaylı değerlendirmek durumunda kalıyorlar.
Üretim
Toz boya üretimi ( bakınız şekil 1 ) hammaddelerin “plastik’’ bir karışım elde etmek üzere farklı aşamalardan geçmesini kapsar. Bu karışım mikronize edilip siklon ayırıcı ile büyük ve ince toz taneleri ayrılmadan önce soğutularak küçük plastik parçalara ( chip ) bölünür.
Şekil 1 : Toz Boya Üretim İşlemi Genel Akışı ( Kaynak : Neumann and Esser )
Son olarak ince toz, filtre torbasından gelebilecek toz topakları veya iplik gibi ve üretim akışı esnasında polimerize olan iri taneler gibi istenmeyen maddeleri ayırmak için elekten geçirilir. Bu aşamada tozları elekten geçirmek sadece doğru tane boyutundaki parçacıkların dolum hattına geçmesini sağlar. ( bakınız şekil 2 )
Şekil 2 : Neumann and Esser tarafından gerçekleştirilmiş tipik bir uygulama. Eleme işlemi genellik ile dolum hattı öncesi siklon altına konumlandırılır.
Bu işlem direkt olarak kaliteye ve boyama aşamasında filmin kalınlığına etki edeceğinden dolayı çok önem arz etmektedir. İnce kat yetersiz boyaya, kalın kat ise boşa harcanan paraya sebep olur.
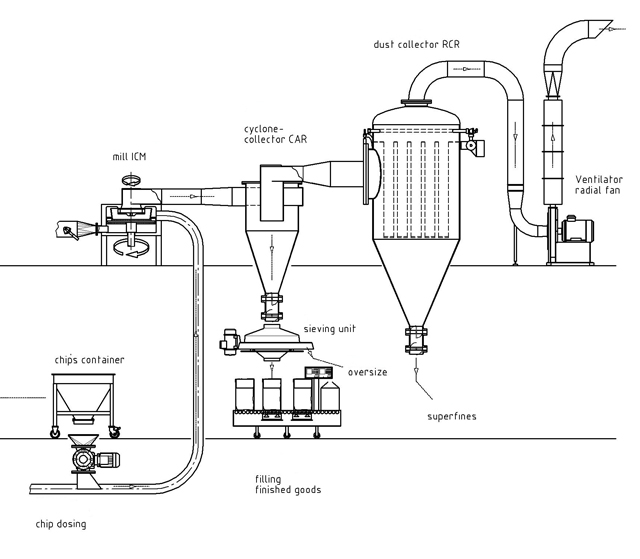
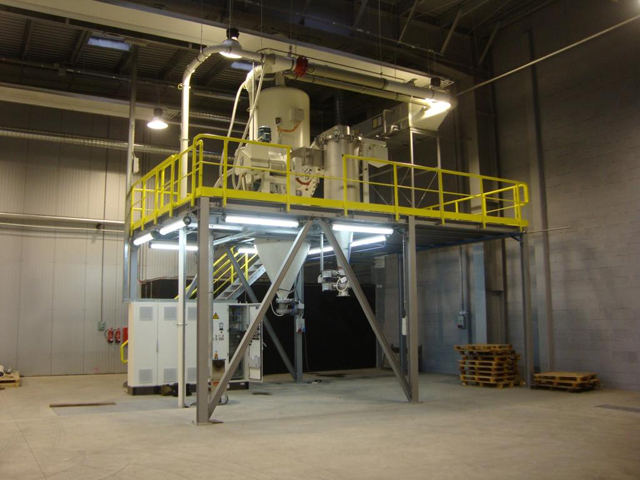
Geleneksel Eleme Yöntemleri – Karşılaşılan Problemler
Toz ile boyama süreçlerinde tozlar statik yük tutmak üzere tasarlandığı için, elekten geçme aşamasında elek gözeneklerinin tıkanması ürün kalitesini ve eleme kapasitesini riske atar ve problemlere sebep olur.
Bu problemi önlemek için bazı üreticiler sistem dışı (offline) eleme yoluna gitmişlerdir ama bu yöntem de kalite kontrol problemlerinin ortaya çıkmasına sebep olmuştur. Diğerleri bir rotorun tozun elek gözeneklerinden geçmesini zorlarken merkezkaç etkisi yaratan döner ( rotary ) elekleri kullanmayı tercih etmektedirler. Ancak elekten geçirilme sürecinde iri taneler de geçebildiği için, bu işlemle de ürün kalitesi riske girmektedir.
Döner ( rotary ) elekleri kullanmanın bir diğer sakıncası ise, çoğunda kırılmaya ve yırtılmaya yatkın naylon elek tellerinden kullanılmasıdır. Serbest akış ile beslenen vibrasyonlu ( titreşimli ) elekler tercih edilen bir yöntemdir çünkü sadece elek aralıklarından küçük parçacıkların dolum hattına geçmesine izin verirler.
Uzun yıllardan beri yay montajlı elekler kullanılmaktadır, ancak bu elekleri demonte etmek zordur ve bu da temizlik süresinin uzamasına yol açar. Pazardaki son değişikliklerle beraber üretimde aynı ürünün üretim miktarları azalırken faklı ürünlerin sık sık üretilmesi ihtiyacı oluşmuştur. Bu da üretimde bakım onarım sürelerinde ve ekipman temizliği maliyetlerinde önemli ölçüde artışa yol açmıştır. Böylelikle üreticiler sürecin yetersizliklerini görerek alternatif çözüm arayışı içine girmişlerdir.
Çözüm – Kompak Tasarım ve Kolay Temizlenen Elekler
Yakın geçmişte 75. yılını kutlayan Russel Finex, toz boya endüstrisine uzun yıllardır hem eleme çözümleri sağlayıp hem de karşılaşmış oldukları sorunları anlamak ve bunları hızlı bir şekilde çözmek açısından önemli derecede deneyim kazanmıştır. Russel Finex, yeni ürün geliştirme ve teknolojideki yeniliklere yatırım yaparak bu uygulama için en nihai eleme çözümünü bulmuştur. Russel Compact Sieve® ve Vibrasonic Deblinding® Sistemi birleştirerek, en etkili eleme sistemi elde etmiştir.
Russell Compact Sieve®; isminden de anlaşılabileceği gibi; diğer vibrasyonlu eleklere göre kapasitesinin çok daha yüksek olmasını sağlayan kısa yapısı, dikine ürün giriş ve çıkış tasarımına sahiptir. Bu küçük boyutlardaki elekler artık birçok sektörde kullanılan en yaygın eleme çözümleri haline gelmiştir. Üretimde boş alanların genelde sınırlı olmasından dolayı, şirketler bu süreçte az yer kaplayan ünitelerin olmasını tercih ediyorlar ama karlılığı düşürebilecek dar boğazların da olmaması için kapasite seviyesinin yüksek kalmasını garantilemek istiyorlar. Motorun yana monte edilebilmesi bu ünitelerin ara platforma veya mobil şaseye monte edilerek dolum hattının elek altının hemen altında olmasına imkan vermektedir ve yer kazancı sağlamaktadır.( bakınız şekil 3 )
Şekil 3 : Russell Compact Elek, B.A.E . Jotun fabrikası dolum hattı öncesi
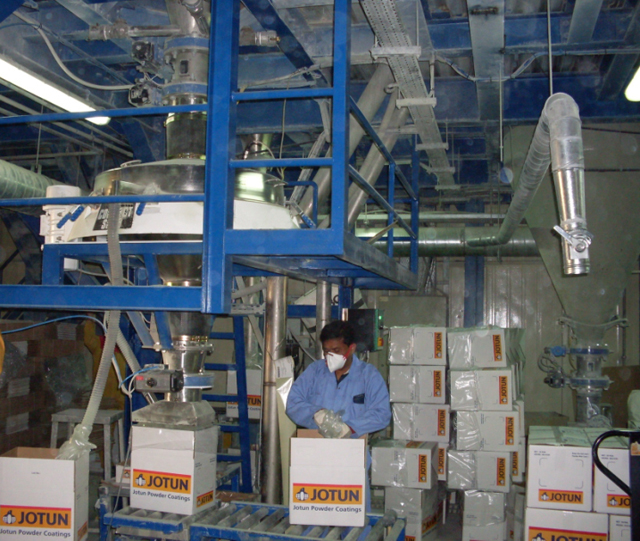
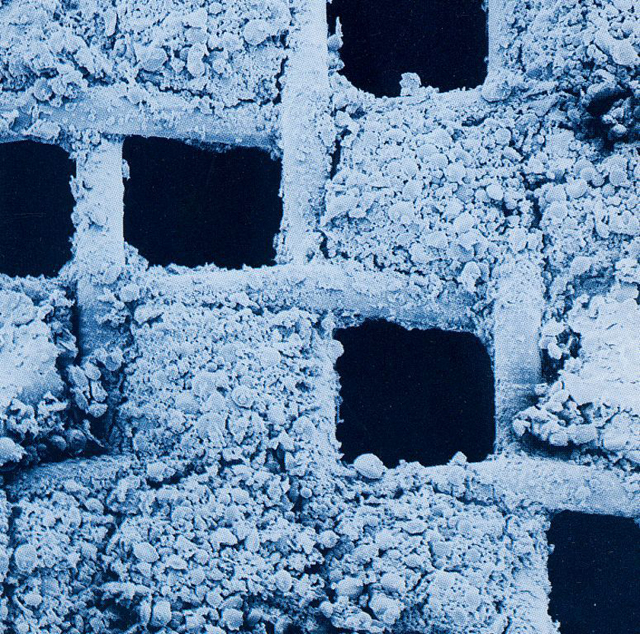
Bu eleklerin en temel özelliklerinden biri de kolay temizlenebilir bir tasarıma sahip olmasıdır. Renk değiştirirken ürünlerin bir birine karışmasını engellemek için işlem hattının çok iyi bir şekilde temizlenmesi gerekir. Demonte edilmesi ve temizlenmesi çok zor olan geleneksel yay montajlı ya da döner ( rotary ) eleklerin aksine Russel Compact Sieve®, herhangi alete ihtiyaç olmadan birkaç saniyede demonte edilebilir kelepçe sistemine sahiptir. Ayrıca malzeme ile temas eden parçaların az sayıda olması ve bu parça yüzeylerinin de pürüzsüz bir yapıda olmasından dolayı bu elekleri temizlemek zahmetsizdir.
Jotun A/S states’in proje müdürü Idar Larsen, “Russel Compact elekler ile en küçük bir ürün kontaminasyon riski dahi ortadan kaldırılmıştır. Değiştirdiğimiz döner (rotary) birimlerine kıyasla, bu elekleri demonte etmesi ve temizlemesi çok kolay. Ayrıca, daha önce sık sık yaşadığımız, naylon elek tel parçacıklarının ürünün içine kaçması problemini de döner (rotary ) elek makinelerinin kaldırılması ile ortadan kaldırmış olduk.” demiştir
Toz boyanın doğası gereği, statik şarj çoğu zaman elek tellerinde toplanarak elek örtüsünün tıkanmasına yol açabilir. Bu da kullanılan elek yüzeyinin ve elek kapasitesinin düşmesine ve üretim oranlarının azalmasına yol açar. ( bakınız şekil 4 )
Şekil 4 : Eleme işlemi esnasında partiküller paslanmaz çelik elek telleri arasına birikerek gözenekleri kaparlar. Ultrasonik elek temizleme sistemi ile bu problem ortadan kaldırılmıştır.
Birçok firma, elekleri manüel olarak temizlemeye çalışır ama bu hatalı muamele veya temizleme yöntemi elek tellerinin sık sık hasar görmesine yol açar. Bazı diğer firmalar, yukarı ve aşağı zıplayan elek tellerine çarparak tıkanmalarını engelleyen disk ya da top gibi mekanik çözüm barındıran eleme sistemleri kullanmaktadırlar. Maalesef disklerin bu hareketi de elek tellerine zarar vererek ömürlerini kısaltır. Daha da önemlisi bu parçalar aşındıkça, içlerindeki plastik ya da lastik parçalar düşerek elekten geçirilen tozların içine karışarak kontamine olmasına yol açabilir.
25 yıl önce ultrasonik sistemi ilk icat edenler, Russel Vibrasonic Deblinding Sistemi ile elek tellerine ultrasonik frekans uygulayarak titreştirirler. ( bakınız şekil 5)
Şekil 5 : ATEX onaylı Vibrasonik prob Zone 20,21,22,0,1,ve 2 tüm Russell Eleklerine adapte edilebilir
Bu da yüzey gerilimini yok ederek paslanmaz çelik tellerin sürtünmesiz olmasını sağlar. Bu sistemin mekanik ya da aşınan bölümlerinin olmamasından dolayı gözeneklerin hasar görme ya da ürünlerin kontamine olma riski yoktur. Bu sistem gözeneklerin kapanmasını ya da körleşmesini engellediği için, eleme kapasitesinin ve verimliliğin üretim süreci boyunca sabit kalmasını sağlar. Manüel işlemin azalmasına bağlı olarak da temizlik için harcanan süre önemli ölçüde azalır ve elek ömrünün uzamasına yol açar. Bu aynı zamanda daha az iyi tozun boşa harcanması demektir.
Hem Compact Elek hem de Vibrasonic® sistem 0 ve 20 dahil tüm Zone’larda çalışabilir şekilde ATEX onaylıdır. Ayrıca üretim oranlarını muhafaza etmek için var olan değirmen sistemleri ile eşleştirilebilirler. (Bakınız şekil 6’daki tablo)
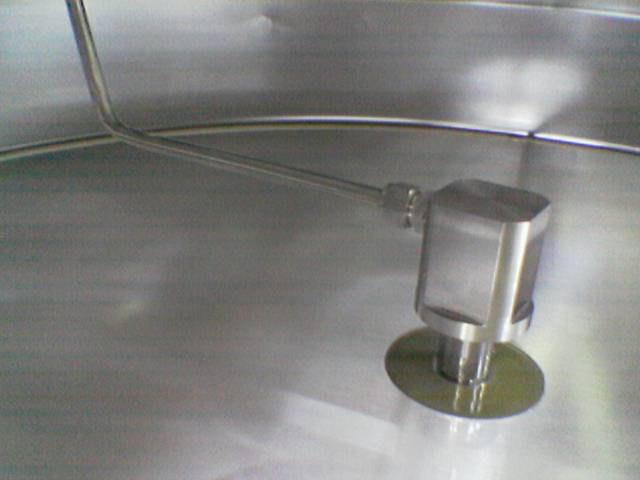
Elek Modeli |
Değirmen Ölçüleri |
Elek Ölçüsü ( µm) |
Kapasite (t/saat ) |
Compact 1200 |
ACM 50 - 60 |
125 |
1,5 |
ICM 48 - 96 |
150 |
2 |
|
Compact 900 |
ACM 10 – 30 |
125 |
0,5 |
ICM 24 -38 |
150 |
0,8 |
|
Compact 600 |
‘Off-line’ geri dönüşüm |
125 |
0,25 |
150 |
0,4 |
“Russel Compact eleklerin pazara sürülmesiyle eleme verimliliğinde önemli ölçüde artış gözlemlenmiştir, bu da bize önemli avantajlar sağlamıştır. Bu da demek oluyor ki sadece iri taneler elek üstü bölümünde toplanmaktadır” der. Daha önce kullandığımız geleneksel döner elek makinelerinde iyi kalitedeki ürünler de iri tane bölümünde toplanırdı. Larsen; “Şu anda pazardaki en iyi teknolojiye sahip olduğumuzu düşünüyoruz” diye sözüne son verir.
Toz boya üreticilerinin bu sürekli artan rekabet ortamında hayatta kalabilmeleri, ürün kalitesini muhafaza ederek karlılığı maksimumda tutmalarına ve üretimdeki verimliliği artırabilmek için yeni teknolojileri kullanmalarına bağlıdır.
75 yılı aşkın bir süredir Russell Finex, ürettiği ve tedarik ettiği filtreler, separatörler ve elekler ile ürünün kaliteli olmasını, üretim verimliliğinin artmasını, çalışanların sağlığının korunmasını, toz ve sıvı maddelerin kontaminasyonsuz olmasını sağlar.
Russell Finex, gerçekleştirmiş olduğu bir çok uygulama ile toz boya, gıda, ilaç, kimya, plastisol, yapıştırıcı, boya, metal tozu, plastik ve seramik gibi bir çok sektöre dünya genelinde hizmet vermektedir.